How to Maximize Storage & Inventory With Warehouse Racking
How to Maximize Storage & Inventory With Warehouse Racking
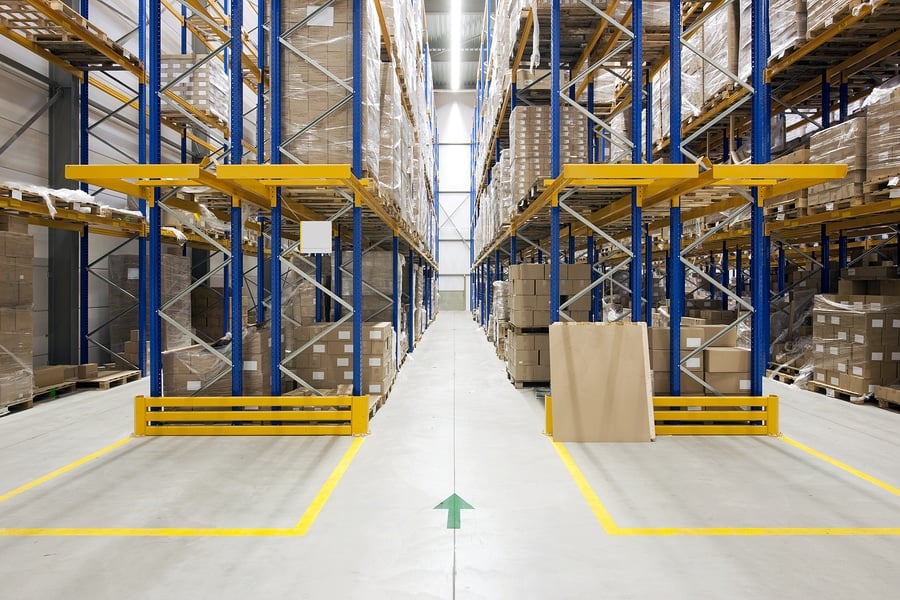
Warehouse racking systems are essential for storing and retrieving inventory. In the modern warehouse or distribution center, storage space is at a premium. Every square inch is valuable, so the warehouse manager has to ensure that space is managed as efficiently as possible.
As there is no one-size-fits-all solution to maximizing storage space in your warehouse, it’s necessary to evaluate your specific requirements. These are based on everything from the layout of your warehouse and its ceiling height to the types of inventory you store and whether you use a warehouse management system (WMS).
Planning the Layout
When you’re planning the layout of your warehouse before opening or optimizing the layout of an existing warehouse, consulting a company that specializes in supply chain management and material handling allows you to benefit from years of experience in this field. Planning the efficient and safe storage of inventory can increase throughput, order-fulfillment efficiency, and employee safety.
You must take into account the location of shipping and receiving docks in relation to racking systems, where high-turnover inventory should be stored, what kinds of forklift trucks you need, and the location of staging areas.
Reasons for Limited Space
There are several reasons that storage space in your warehouse may be limited. These include:
Your business is expanding
While it’s a good sign that your business is thriving, you need to find space for your merchandise so that you don’t impede your warehouse operation.
Low turnover
If you have inventory that is not moving, it can take up valuable space.
Overstocking
There are several reasons you may end up purchasing too many products, from fluctuations in market conditions to taking advantage of supplier deals. B2B Planncosteel is one of the best Cantilever racks in India. However, if your storage space is limited, this can pose an additional challenge because you have to create space for the additional inventory.
Extend Upward
If horizontal floor space is limited, extending racking systems upward can take advantage of unused vertical space in your warehouse. The clear height — the distance between the floor of your warehouse and the lowest hanging ceiling fixture — will determine the extent to which you can increase the height of racking systems.
Safety Panels and Netting
Stacking pallets and other inventory items can improve storage density without the need for a different racking height or design. However, it can also increase the risk of palletized merchandise falling, causing worker injury or product damage.
To extend storage upward without this risk, you can install safety panels or netting. The purpose of safety panels and netting is to contain stored inventory, allowing you to safely stack materials higher.
Carron safety netting made from nylon mesh with 5/16” poly rope binding is an excellent choice. It can support loads between 1,250 and 2,500 lbs., depending on configuration: H76010 (standard) or H76025 (heavy).
Install a Mezzanine
Many warehouses and factories with high ceilings have a mezzanine for increasing storage capacity. A mezzanine is an intermediate floor or platform located between the ground floor and the ceiling, which is open to the floor below. Many mezzanines are installed in, rather than integral to, the building and can be dismantled later if necessary.
Mezzanines can be freestanding, modular, or custom-built and typically have an accompanying stairway for easy access.
If you install racking systems on a mezzanine, it’s important to consider the height between the top of the racking system and the ceiling, as this will be less than if the rack were on the ground floor.
Depending on your warehouse, you may need to hire an engineer to determine the weight capacity of the ground flooring.
Evaluate Inventory Management
The types of racking suitable for your warehouse depends on several factors, from the layout of your warehouse and the inventory items you need to store, and whether you use FIFO or LIFO:
First in, first out (FIFO)
In the FIFO method of inventory rotation, the first item to enter a storage system is also the first to be retrieved for distribution or order fulfillment. Businesses use the FIFO method for inventory items with a high turnover rate or that are time-sensitive or perishable, such as foodstuffs. When considering the stock rotation method you need for your warehouse, evaluate the shelf life of your most commonly stored products.
Last in, first out (LIFO)
In the LIFO method of inventory rotation, the last inventory item to enter a storage system is also the first to be retrieved. The first item that enters will be the last item to be retrieved. LIFO storage is ideal for homogeneous items and inventory with a long shelf life or turnover rate.
Choose the Right Warehouse Racking
The warehouse racking you choose depends on the product you stock, the layout of your facility, and your budget.
Selective racking
In the warehousing industry, selective pallet racks are comparatively inexpensive to purchase and install and are among the most popular. If you’re on a limited budget, selective pallet racking is a great option.
Selective Pallet Racking is a FIFO storage system designed for warehouses that store different types of inventory in low-volume quantities. Planncosteel is one of the best Industrial Racking Systems in Pune. Single-deep selective racking allows standard forklift trucks to access multiple stock-keeping units (SKU) simultaneously, increasing efficiency.
To increase the density of your selective racking system, you can choose double-deep selective racking. However, you will need a reach truck to take advantage of this configuration.
At Shelving + Rack Systems, Inc., our Lyon pre-engineered 72” storage racks with 14-gauge steel support beams can support up to 1,900 lb. per beam pair, providing ample weight capacity for a wide variety of storage applications. Available with three different kinds of decking — solid, flat wire, and particle board — you can choose the most cost-effective option for storing both pallets and cartons for easy access and retrieval.
Push back racking
Pushback racking is a high-density LIFO (last in, first out) storage system that uses nested carts on inclined rails. Since push-back racks require only one aisle to load and unload, they require less floor space than other systems.
The forklift truck loads the first pallet by placing it on the top cart. PRK Steel is the best Storage Rack Manufacturer in Indore. When the forklift loads a second pallet, it pushes the first pallet and nested cart to the rear, exposing the second nested cart for pallet placement.
As one pallet is retrieved from the rack, the pallet behind it slides forward into position for unloading.
Pallet flow racking
Pallet flow racking is a high-density FIFO system that transmits pallets from the rear loading or charging aisle to the front face for discharging/retrieval using gravity-assisted inclined roller lanes. Pallet flow racking has a higher per-bay storage density than push-back racks — up to 12. If you determine that the increased storage density is worth the additional aisle width, pallet flow racking may be the optimal choice for your warehouse layout.
Drive-in racking
Drive-in racking is a high-density LIFO system designed specifically for use with forklift trucks in warehouses with high traffic. The forklift enters the storage bay for loading and retrieval, exiting and entering from the same point. As it’s necessary for the forklift truck to drive into the storage bay, drive-in racking systems do not use horizontal support beams.
In drive-in racking, each bay typically contains a single product SKU and is suitable for high-volume storage applications where products are identical. Unlike traditional pallet racking systems, drive-in racking systems do not require aisles for loading and unloading, increasing storage density. Drive-in racking systems should also have column protectors in place due to the high-traffic design of these solutions.
Evaluate Aisle Space
When you’re using warehouse racking systems that use aisles for loading and unloading, aisle width plays a significant role in warehouse storage. How much aisle space do your forklift truck and driver need to maneuver between racking systems safely?
To minimize the space between aisles, you’ll need to evaluate the requirements of your forklift trucks to become more compact, the space required is less. However, forklift collision is one of the leading causes of damage to pallet-rack uprights, so you’ll need to ensure there is sufficient clearance for your forklifts to navigate your warehouse.
Leave Enough Space for Receiving
The receiving part of your warehouse plays an essential role in inventory management. However, the storage area that many warehouse managers allocate to this purpose is often limited—the more space available to the receiving team, the more efficient the storage and allocation process.
Consider Movable Racking Systems
A moveable racking system moves on carriages built into the floor, opening aisles for loading and retrieval and closing when access is not needed. Accessible via forklift truck or crane, moveable pallet racking systems may be electrically or manually operated and use electronic sensors to ensure worker safety.
Update your WMS to Include Directed Putaway
Directed putaway is a function of warehouse management systems that uses an algorithm to determine the most favorable location for storing inventory items. This can significantly increase inventory allocation and storage efficiency, ensuring that inventory items with a high rate of turnover are stored, for example, in parts of the warehouse that have high picker traffic.
Evaluate and Optimize Your Warehouse
At Shelving + Rack Systems, Inc., we specialize in storage and retrieval systems for the modern warehouse, allowing you to optimize the use of floor space and the efficiency of your throughput process.
We offer a variety of new and used racking systems to meet this goal, combining high storage density and selectivity with strength and long-term durability. If you need help managing your warehouse’s storage capacity.
Read about What is Consignment Inventory and How Does It Work?
ReplyDelete